I wish I had more to update, but I really have not worked on the car much this whole summer. Just been driving it! I had a few small problems, but nothing that sidelined me for more than a day. One of my chargers died, good thing I have two of them! It's a burned fuse holder, an easy fix I think, but I haven't taken it to anyone to look at yet. For now I'm just sticking with the other charger. The downside is that it's a very slooooow charger, but it works OK. I also had a wire break in my charging cable, that was also a quick fix (cut off and replace a plug). I also have some weirdness in the power door locks, and one of the rear windows doesn't always work, but those are just 15 year old car problems, not related to it being electric.
Just for kicks, I went online to the PG&E website and compared our electric usage and costs for September 2011 (the last month before I started driving the EV) to September 2012. Our electric cost went from $145 last year to $199 this year. So instead of spending $238/month on gas, I spent $54 on electricity. A $184 savings! This assumes 10k mile/year, $4/gallon gasoline, and 14mpg which is what I used to get in the Odyssey in around town driving (the car the Saturn replaced).
Here's a picture of my car at a public charging station nearby. As of now most of these are free (well, not really free I guess, since taxpayers paid for them and their electricity, thank you everyone!) and I plug into them every once in a while if I happen to be there anyway. There's only one on our city, but 4-5 within 20 miles or so one city over. Once I get a higher power charger (it's hardly worth it right now, three hours of charging only gets me about 10 miles of range) I plan to use the charging stations more often.
Yes, it needs a wash...
Saturn 'EV2' electric car conversion
The ongoing story of life with a 100% electric car
Wednesday, October 3, 2012
Tuesday, July 10, 2012
New Motor Mount
It's been quite a while since an update! whoops... I've done lots of little things, one pretty big fix (new upper motor mount) and have been driving the car most every day for the last few months. Here's the big fix, I replaced the upper motor side mount with a stock Saturn mount and a new steel bracket (made of a few pieces of welded up angle iron) which has really made the motor more solid. I was, and still am having an issue with excess driveline backlash, this new mount really helped. I've still got too much motor/driveline movement going on though. I'm not sure if it's in the mounts or the suspension, but I have a suspicion it's mostly motor mounting. Anyway, quite drivable, but it can be lurchy if I'm not careful to preload the driveline before pulling away from a stop.
here's the new mount, needs paint...
here's a view with the component tray down in position,
I had to do a little trimming, and moved the contoller over about 2 inches (it's not installed in this photo). Fortunately there was enough room to do it without major changes, just had to shift over some wiring and the heater controls box.
While I was doing this, I also upgraded the other mounts with polyurethane inserts to replace the stock rubber. One was pretty torn up, the weak motor side mount was putting a lot of extra strain on the other mounts. here's the before picture of the torn up insert,
and the after, with the new insert,
much more solid now.
With the new more solid mounts, I also cranked up my controller to 750a to the motor. Which caused the clutch to slip... I've turned it back down to 650a which seems ok for now, at some point when I have the motor out again I'd like to put in a racing clutch so I can use the full power of my controller. But for now I'm set at 500amps battery side, and 650amps motor side and it drives very well. No problems keeping up with cars on the road. And it's very quick off the line, easily spins the wheels in 2nd gear from a standstill.
Only other big fix was a busted shifter cable bushing. Not EV related, just 20 year old car related. :-) Fortunately it was an easy fix, I temporarily fixed it with zip ties and ordered a new cable bushing from ebay and had it fixed in a few days.
Also, I have still not done anything about the weak battery cells. I just left them all as they are, and it's doing OK. I'm definitely getting more voltage sag (and thus lower efficiency) than I ought to have, but there's still plenty of range for my needs. I have a reliable 45 mile range which is plenty for me on a daily basis. I have some ideas of how to do some testing, but for now I'm just driving it. I do think I'll buy a pair of extra cells here soon (I think at some point I'm going to piggyback a few cells, and add 2 new ones to the system) since the 130ah cells I'm using have been discontinued and I feel like I ought to buy them now before I can't get any more!
That's all for now, fwiw I have now driven about 5000 all electric miles with this car, and am driving my gasoline powered van 1-2 times a month when my range (or carrying capacity) needs exceed those of the electric Saturn.
here's the new mount, needs paint...
here's a view with the component tray down in position,
I had to do a little trimming, and moved the contoller over about 2 inches (it's not installed in this photo). Fortunately there was enough room to do it without major changes, just had to shift over some wiring and the heater controls box.
While I was doing this, I also upgraded the other mounts with polyurethane inserts to replace the stock rubber. One was pretty torn up, the weak motor side mount was putting a lot of extra strain on the other mounts. here's the before picture of the torn up insert,
and the after, with the new insert,
much more solid now.
With the new more solid mounts, I also cranked up my controller to 750a to the motor. Which caused the clutch to slip... I've turned it back down to 650a which seems ok for now, at some point when I have the motor out again I'd like to put in a racing clutch so I can use the full power of my controller. But for now I'm set at 500amps battery side, and 650amps motor side and it drives very well. No problems keeping up with cars on the road. And it's very quick off the line, easily spins the wheels in 2nd gear from a standstill.
Only other big fix was a busted shifter cable bushing. Not EV related, just 20 year old car related. :-) Fortunately it was an easy fix, I temporarily fixed it with zip ties and ordered a new cable bushing from ebay and had it fixed in a few days.
Also, I have still not done anything about the weak battery cells. I just left them all as they are, and it's doing OK. I'm definitely getting more voltage sag (and thus lower efficiency) than I ought to have, but there's still plenty of range for my needs. I have a reliable 45 mile range which is plenty for me on a daily basis. I have some ideas of how to do some testing, but for now I'm just driving it. I do think I'll buy a pair of extra cells here soon (I think at some point I'm going to piggyback a few cells, and add 2 new ones to the system) since the 130ah cells I'm using have been discontinued and I feel like I ought to buy them now before I can't get any more!
That's all for now, fwiw I have now driven about 5000 all electric miles with this car, and am driving my gasoline powered van 1-2 times a month when my range (or carrying capacity) needs exceed those of the electric Saturn.
Wednesday, April 4, 2012
minor update
minor update here, just some small stuff.
I've got the EVDisplay up and running, it's sweet! I am using the wireless bluetooth to android version sold by emotorwerks.com. I posted some pictures of the current sensor and the bluetooth sender box in an earlier post, this is what it looks like on my DroidX on the dash of the car.
and a closeup of the display.
it is very customizable. I have it set up with a big analog battery current gauge, a small analog 'fuel' gauge, and then have digital readouts for voltage, Ah remaining, Wh/mi, and battery current (redundant, but the digital gauge lets me see small changes in charging voltage). Obviously on a larger tablet you could display more info, but this is perfect for what I want!
a nice thing about having an amp-hour counter is that you can do partial charges and still have an accurate knowledge of how much range you have left in the pack. With the Lithium batteries, you cannot just use voltage like you can with lead acid batteries, since all the power is in such a small range of voltage (pretty much between 3.2 and 3.4v per cell)
It's also super cool that the Bluetooth range is enough that I can have my phone in the house plugged into the wall and it still gets the signal so I can monitor the state of charge when charging from the kitchen! Just handy for those times when I want to do a partial charge during the day.
In that first picture above, you can see a box with three toggle switches in it just above the radio (the box is currently wedged in place with a paper towel, I'll pick up some foam tape to mount it soon...). Only one of those is hooked up right now, it's my 'stealth mode' switch, it kills the relay that runs the motor fan and my brake vacuum pump so I can move about silently in parking lots. :D
The vacuum pump has also been moved, it now lives down on the old front battery rack with the motor blower, mounted onto a cutting board (for now) that is mounted to the rack with radiator mounts (rubber isolation mounts with bolts on each side) to reduce vibrations transmitted to the car. While doing this, I also eliminated the vacuum reservoir chamber, I found it's not really needed. The only change is that the pump now cycles on every 1-2 braking 'events', instead of the every 2-3 that it did with the big PVC tank.
here it is looking forward, you can see the little 'muffler' on the exhaust side of the vacuum pump, I don't really think it does much muffling though... and the big K&N filter on the motor blower.
this photo shows the routing of the hose from the pump to the master cylinder. And also just a general underhood view of how it looks these days.
The final thing I've done is to get my tachometer working! However, it's not accurate... My speed sensor on the motor sends a 4 pulse per revolution signal to my controller, but the factory tach requires a 6 pulse signal, so it reads low. No big deal, I just know that my redline of 5000 rpm is 3500 on the tach. I may make a custom overlay at some point, but that would require a lot more disassembly to get to the actual gauge face.
It turned out to be real easy to do, I tapped into the sensor signal to the controller, and hooked it up to the old ammeter wire (which I'm no longer using) which already runs through the firewall up to the back of the dashboard. All I had to do was remove the upper dash pad, two bolts and a few clips (which broke, of course...). Found the wire leading to the tach, snipped it, and connected it to the signal. Done! it's the white wire zip tied to the harness below. While I was in there, I cut the wire going to the 'service engine soon' light, which has always been on. Since there's no more engine to service, I figure I don't need that any more. :D
here's a shot of the tach working, and the comparison with the actual motor speed on my laptop reading direct from the controller.
That's it for now, lots more little stuff on the way, and hopefully a big rebuild of the motor mounts soon.
Friday, March 23, 2012
Battery Racks
I'm back on the road, just slow on updating the blog! Alright... short summary here. I finished testing all the batteries, there are about 12 that are a bit weak, 4 tested pretty badly. However, none are bad enough to need to do anything about it right now. I'm going to do some testing later on to see how much replacing a few of the worst cells would help, but not right now. I'm just happy to have it back together and driving again! Basically I pulled all the batteries for testing, and while they were out I re-designed the battery racks to hold the cells more securely, then re-installed the batteries.
here's a longer version of what I did to modify the battery racks:
I bolted angle iron to the floor of the trunk to hold the upper shelf of batteries. These are just attached with sheetmetal screws, not real structurally but they don't need to be. The hold down will not attach to these pieces, they just keep the cells level and aligned.
Here’s sort of a side shot, you can see my standoffs for the
copper bar. It’s just a long bolt with
three nuts to stand it off far enough. I
was pretty meticulous about tightening all the nuts up against each other, but I’m definitely going to keep an eye on
this. I don’t love the design I came up
with here…
here's a longer version of what I did to modify the battery racks:
I bolted angle iron to the floor of the trunk to hold the upper shelf of batteries. These are just attached with sheetmetal screws, not real structurally but they don't need to be. The hold down will not attach to these pieces, they just keep the cells level and aligned.
Next is the upper hold down. I built it out of angle iron and brought it down to a local welder to weld it up. He's a good guy, owns a local muffler shop. I've had a few things welded up there now, quick and easy for a few bucks. this picture shows it mocked up with the two outermost batteries in place.
The upper 12 batteries are strapped in sets of 4, then after
installing into the rack I ran one big strap around all 12 to keep them from
sliding relative to each other (that final strap is not shown in the following
photo, I added it later). I don’t think that
strap was really needed, but why not?
Anyway, I’m happy with how the rack came out, on the rear side I used
battery hold down J bolts that I picked up at the local auto parts store, and
on the front side I used 12” long allthread through the floor. It’s double nutted with a fender washer under
the floor, and you can see the upper rack in the first photo below, I think it
came out quite nice!
In addition to the modified racks, I'm also rewiring the trunk. I've added a fuse and an amp counter (the EV version of a fuel guage) and moved a bunch of stuff around. The bulk of my time was spent making the component boards
and figuring out how to lay everything out, and mounting the stuff to the
boards. It took several iterations till
I got it right… definitely a 2 steps
forward, 1 step back process. In the end
it looks good, and keeps everything neat and up out of the way. In the below photo, you can see all the stuff
on it. From left to right, the EV
Display Bluetooth sender, the MiniBMS head end unit (with the EV Display Cat5
cable coiled below it), the EV Display sender unit, the main pack fuse, and
just below the fuse is a terminal strip with 160v+, 160v-, 12v+, 12v-, and Ign
on it for the EV Display and BMS. I’ve
also wired the charger outputs up to the terminal strip too. On the negative side I’m tapped into the pack
between the main fuse and the EV Display sensor. On the positive side, I’m hooked up to the
most positive battery terminal. Last but
not least, on the far right is the main pack disconnect, a large circuit
breaker. Eventually I’ll run a bicycle
derailleur cable from the breaker, under the carpet and up to the driver, but
haven’t done that yet.
Here is a close up of the EV Display sender unit (the amp counter). I wrapped the copper bar in tape to make it a
snug fit (just to eliminate any rattling) and screwed the circuit board to my
component board with nylon spacers cut to length. It’s pretty solid.
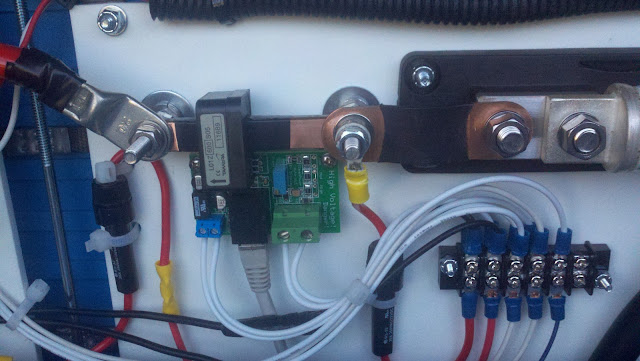
once the component boards were done and wired up, I began
dropping in the lower set of batteries.
At first I banded the cells, but quickly realized 2 things. One: this was not going to work! It’s too tight a fit into the trunk rack, and
even 4 cells together were too heavy to work with here. Two:
It would be pretty easy to restrain the cells mechanically, so there is
really no need for the banding anyway!
So… with that figured out I just installed the cells one at a time. It’s a good snug fit front to back, with a
1/8” sheet of HDPE lining the rack there is minimal movement allowed.
Side to side there was about 2 inches on each side, so I dropped a piece
of angle iron down in the bottom of the rack and bolted it down. Here’s an attempt at a photo of this, though
it’s a tough spot to get a picture.
With the bottom of the cells locked in, I make a simple side
brace out of a small angle and a strip of flat steel. Tough to describe, but the pictures below
shows what I did pretty well.
Now the cells are locked in side to side, and can only
wiggle slightly front to back, I’m pleased with the layout! I again lined the sides of the rack with 1/8”
HDPE just to keep grime and water out, and used a firm 2” thick window sealing
type foam between the batteries and the plastic to keep it in place.
To restrain the cells vertically, I decided on metal straps
over the top of the cells. I don’t love
this part of the design, only because there is really no downward force at all
on the middle 5 or so cells. It’s
basically there to prevent batteries flying around in the case of collision
though, and it’s certainly strong enough for that. Here’s a photo of the cells with the straps
in place prior to wiring up the batteries.
This next part took a few days… just because I can’t seem to
find a solid chunk of time to work on the car these days. Nothing difficult, just a bit tedious, and
unforgiving if a mistake is made! I
installed all the BMS boards (Battery Monitoring System) and cell interconnects. For the cells that needed to connect end to
end (instead of the normal side to side) I ordered a few braided interconnects
from evworks.com and they work great, but again I’m not loving the metal straps
holding down the cells. The braided
interconnects lay down right on top of them.
I covered the bar with a strip of duct tape, then wrapped the
interconnects with 2 layers of electrical tape to prevent shorting anything
out. At the end of the day, this is what
it all looks like.
Here’s a shot from a bit further back that shows the whole
trunk.
I still have a ton to do that I didn’t get to, like
redesigning the motor mounts and moving some stuff around up under the
hood. I also need to make a cover for
the batteries so I can actually use the trunk.…
oh, I also didn’t paint the
metal parts yet, because it’s been rainy and really windy for the last few
weeks, and I have to paint outside. This
summer I’ll just have to pull them out for paint I guess. Everything that needs painting can be removed
without removing the batteries, so it’s not that bad.
I also didn’t do anything to address the weak cells, just
wired them all back in. I did put all
the weak ones up in the upper battery rack where it’s easier to get to them
later. I do plan on doing some
experimenting with eliminating the worst cells to see how that affects relative
voltage sag under load, but that stuff is all going to have to wait a while,
I’m just happy to have it up and running again!
Especially as gas is edging up towards $5/gallon around here.
Wednesday, January 25, 2012
Battery Testing
I got the Big Red Van back from the shop last
week and it seems to be running fine. So... with that I'm putting it back into
daily use and have started pulling batteries out of the Saturn. My plan
is to cycle every cell to determine their actual amp-hour (ah) capacity and
internal resistance (ir). I bought a little charger that is really made
for remote control car/airplane type batteries, designed to quick charge them,
but it will work very well for what I need as well. It's called the Powerlab 6 from Revolectrix, and it will discharge and charge the cells at up to 40a,
and create cool looking graphs. Fairly unique is it's ability to
calculate the cells internal resistance, which is a strong indicator of health.
Each cell will take 7-8 hours to cycle.
3. Length of time at
CV. The good cell gets full in about 20 minutes after hitting 3.60v, the weak
cell sits there for over 45 minutes.
Yes, this will take me a few weeks to do since
there are 48 cells, I figure I'll be lucky if I can get 2-3 done per day. But I
am also going to pull the motor/trans out and re-do some things in the car so
it's not just lost time.
As of now, I've got 14 cells done. It's not
stellar news in that quite a few cells are below spec, but it's about what I
expected based on the voltage sag I've recorded while driving. What is
interesting is that there are some cells that are excellent, some that are
normal, and some that are weak, but there is no pattern to where they are in the series string of batteries.
A good cell will be right next to a weak cell, quite randomly. It
makes it hard to believe that any kind of mistreatment caused the cells to degrade,
perhaps they were just mismatched from the factory? Typically not the
case, but I'm not sure how to explain such a wide variance. Some cells
are testing over 135ah, others are below 125ah. Internal resistance
numbers are varying from 0.5mohm to 1.2mohm.
Below is a picture of the
setup, there is a 12v deep cycle battery connected to the Powerlab 6, connected
to the battery cell. I've got a power supply on standby in case it needs it on
the charging side, and the laptop is connected to the PL6 via USB and logs all
the data. The fan is there to keep everything cool.
It's really cool to do these tests, I've seen all
the battery charts before, but it's a whole different understanding of the
cells to actually create the charts. Here
are two volts vs. time files for cells. The top one is a good cell (139ah, 0.5mohm) and the bottom one is a weak cell (124ah, 1.2mohm). Notice the differences:
1. sharpness of curve at end of discharge/charge
cycles. The weak cell is much more gradual.
2. Difference in voltage between the two shelves.
The good cell holds a higher voltage on discharge, and charges at a lower
voltage on the charge side.
Thursday, December 29, 2011
dead battery
just back from a week's vacation, despite disconnecting the 12v battery, and despite charging it up a few hours right before leaving, it was down to 5v when I returned... Not a problem with the car, just a weak battery. It should be able to sit disconnected for a week without going dead. Anyway, I've found I can easily jump-start it by touching a quarter across the DC/DC contactor, which sends 13v from the 160v main pack to the aux battery and gets everything up and running.
In other news, I've begun tearing the upper motor mounts a little bit. A redesign has already happened in my head, just need to make it happen in the car now... Basically I want to replace the upper mounts which are simple cylindrical rubber vibration isolation mounts with the original beefy rubber engine mount that was in the car. I've ordered the parts I need, but it will require fabricating a new end plate to connect the motor to the new mount. And will require pulling the motor/trans out again. That's ok, there's a few other things I want to do in there too that will be a lot easier with it all out.
Next update will probably be in a few weeks, I'm not going to tear it apart until after the new year, and after I have a chance to get the Big Red Van's transmission looked at (it's slipping a bit). In the meantime, I've lowered the motor amps to 350a to save from doing more damage to the upper mount.
In other news, I've begun tearing the upper motor mounts a little bit. A redesign has already happened in my head, just need to make it happen in the car now... Basically I want to replace the upper mounts which are simple cylindrical rubber vibration isolation mounts with the original beefy rubber engine mount that was in the car. I've ordered the parts I need, but it will require fabricating a new end plate to connect the motor to the new mount. And will require pulling the motor/trans out again. That's ok, there's a few other things I want to do in there too that will be a lot easier with it all out.
Next update will probably be in a few weeks, I'm not going to tear it apart until after the new year, and after I have a chance to get the Big Red Van's transmission looked at (it's slipping a bit). In the meantime, I've lowered the motor amps to 350a to save from doing more damage to the upper mount.
Thursday, December 8, 2011
a few little updates... It's been running well, the heater has been fine even in the cold 30 degree mornings lately. And that's just with one element switched on. I can't imagine needing the second one! Though it is garage kept right now, which helps keep it not as cooold overnight. Less to have to warm up.
Anyway, I've been tracking my ah/mile (amp hours per mile) through the controller lately, and I've noticed about a 10% difference between the 30 degree morning run to school, and the 55 degree afternoon pickup. All else is pretty equal but the temp. Not too surprising, batteries don't really like cold weather. Even worse case usage, I've still got an easy 45 mile range without flattening the batteries (you really aren't supposed to take them further than 80% discharged) which is plenty for my daily routine. Best case in the summer should be closer to 60 or so miles.
yesterday I wired the brake vacuum pump through a toggle switch so I can shut it off in parking lots for that cool 'silent EV effect' and for those times when the pump sticks on... I plan to do the same to the motor blower, but it's not nearly as noisy so I'm not feeling quite as urgent about it.
it's getting driven between 20-40 miles every day right now, charging up for what I calculate to be the equivalent of ~$1.30/gallon when normalized against the Honda Odyssey it replaced. And working just fine as my main kid transporter! And this is paying a pretty high $.24/kWh with PG&E, should be able to pretty easily cut this in at least half with either solar, or a dedicated E9 rate meter, or both. Down the road a bit for those...
Anyway, I've been tracking my ah/mile (amp hours per mile) through the controller lately, and I've noticed about a 10% difference between the 30 degree morning run to school, and the 55 degree afternoon pickup. All else is pretty equal but the temp. Not too surprising, batteries don't really like cold weather. Even worse case usage, I've still got an easy 45 mile range without flattening the batteries (you really aren't supposed to take them further than 80% discharged) which is plenty for my daily routine. Best case in the summer should be closer to 60 or so miles.
yesterday I wired the brake vacuum pump through a toggle switch so I can shut it off in parking lots for that cool 'silent EV effect' and for those times when the pump sticks on... I plan to do the same to the motor blower, but it's not nearly as noisy so I'm not feeling quite as urgent about it.
it's getting driven between 20-40 miles every day right now, charging up for what I calculate to be the equivalent of ~$1.30/gallon when normalized against the Honda Odyssey it replaced. And working just fine as my main kid transporter! And this is paying a pretty high $.24/kWh with PG&E, should be able to pretty easily cut this in at least half with either solar, or a dedicated E9 rate meter, or both. Down the road a bit for those...
Subscribe to:
Posts (Atom)