here's a longer version of what I did to modify the battery racks:
I bolted angle iron to the floor of the trunk to hold the upper shelf of batteries. These are just attached with sheetmetal screws, not real structurally but they don't need to be. The hold down will not attach to these pieces, they just keep the cells level and aligned.
Next is the upper hold down. I built it out of angle iron and brought it down to a local welder to weld it up. He's a good guy, owns a local muffler shop. I've had a few things welded up there now, quick and easy for a few bucks. this picture shows it mocked up with the two outermost batteries in place.
The upper 12 batteries are strapped in sets of 4, then after
installing into the rack I ran one big strap around all 12 to keep them from
sliding relative to each other (that final strap is not shown in the following
photo, I added it later). I don’t think that
strap was really needed, but why not?
Anyway, I’m happy with how the rack came out, on the rear side I used
battery hold down J bolts that I picked up at the local auto parts store, and
on the front side I used 12” long allthread through the floor. It’s double nutted with a fender washer under
the floor, and you can see the upper rack in the first photo below, I think it
came out quite nice!
In addition to the modified racks, I'm also rewiring the trunk. I've added a fuse and an amp counter (the EV version of a fuel guage) and moved a bunch of stuff around. The bulk of my time was spent making the component boards
and figuring out how to lay everything out, and mounting the stuff to the
boards. It took several iterations till
I got it right… definitely a 2 steps
forward, 1 step back process. In the end
it looks good, and keeps everything neat and up out of the way. In the below photo, you can see all the stuff
on it. From left to right, the EV
Display Bluetooth sender, the MiniBMS head end unit (with the EV Display Cat5
cable coiled below it), the EV Display sender unit, the main pack fuse, and
just below the fuse is a terminal strip with 160v+, 160v-, 12v+, 12v-, and Ign
on it for the EV Display and BMS. I’ve
also wired the charger outputs up to the terminal strip too. On the negative side I’m tapped into the pack
between the main fuse and the EV Display sensor. On the positive side, I’m hooked up to the
most positive battery terminal. Last but
not least, on the far right is the main pack disconnect, a large circuit
breaker. Eventually I’ll run a bicycle
derailleur cable from the breaker, under the carpet and up to the driver, but
haven’t done that yet.
Here is a close up of the EV Display sender unit (the amp counter). I wrapped the copper bar in tape to make it a
snug fit (just to eliminate any rattling) and screwed the circuit board to my
component board with nylon spacers cut to length. It’s pretty solid.
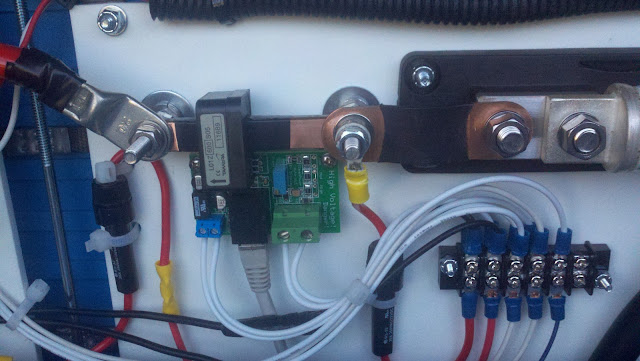
once the component boards were done and wired up, I began
dropping in the lower set of batteries.
At first I banded the cells, but quickly realized 2 things. One: this was not going to work! It’s too tight a fit into the trunk rack, and
even 4 cells together were too heavy to work with here. Two:
It would be pretty easy to restrain the cells mechanically, so there is
really no need for the banding anyway!
So… with that figured out I just installed the cells one at a time. It’s a good snug fit front to back, with a
1/8” sheet of HDPE lining the rack there is minimal movement allowed.
Side to side there was about 2 inches on each side, so I dropped a piece
of angle iron down in the bottom of the rack and bolted it down. Here’s an attempt at a photo of this, though
it’s a tough spot to get a picture.
With the bottom of the cells locked in, I make a simple side
brace out of a small angle and a strip of flat steel. Tough to describe, but the pictures below
shows what I did pretty well.
Now the cells are locked in side to side, and can only
wiggle slightly front to back, I’m pleased with the layout! I again lined the sides of the rack with 1/8”
HDPE just to keep grime and water out, and used a firm 2” thick window sealing
type foam between the batteries and the plastic to keep it in place.
To restrain the cells vertically, I decided on metal straps
over the top of the cells. I don’t love
this part of the design, only because there is really no downward force at all
on the middle 5 or so cells. It’s
basically there to prevent batteries flying around in the case of collision
though, and it’s certainly strong enough for that. Here’s a photo of the cells with the straps
in place prior to wiring up the batteries.
This next part took a few days… just because I can’t seem to
find a solid chunk of time to work on the car these days. Nothing difficult, just a bit tedious, and
unforgiving if a mistake is made! I
installed all the BMS boards (Battery Monitoring System) and cell interconnects. For the cells that needed to connect end to
end (instead of the normal side to side) I ordered a few braided interconnects
from evworks.com and they work great, but again I’m not loving the metal straps
holding down the cells. The braided
interconnects lay down right on top of them.
I covered the bar with a strip of duct tape, then wrapped the
interconnects with 2 layers of electrical tape to prevent shorting anything
out. At the end of the day, this is what
it all looks like.
Here’s a shot from a bit further back that shows the whole
trunk.
I still have a ton to do that I didn’t get to, like
redesigning the motor mounts and moving some stuff around up under the
hood. I also need to make a cover for
the batteries so I can actually use the trunk.…
oh, I also didn’t paint the
metal parts yet, because it’s been rainy and really windy for the last few
weeks, and I have to paint outside. This
summer I’ll just have to pull them out for paint I guess. Everything that needs painting can be removed
without removing the batteries, so it’s not that bad.
I also didn’t do anything to address the weak cells, just
wired them all back in. I did put all
the weak ones up in the upper battery rack where it’s easier to get to them
later. I do plan on doing some
experimenting with eliminating the worst cells to see how that affects relative
voltage sag under load, but that stuff is all going to have to wait a while,
I’m just happy to have it up and running again!
Especially as gas is edging up towards $5/gallon around here.